Start-up team at FAU develop new design process for high-frequency components
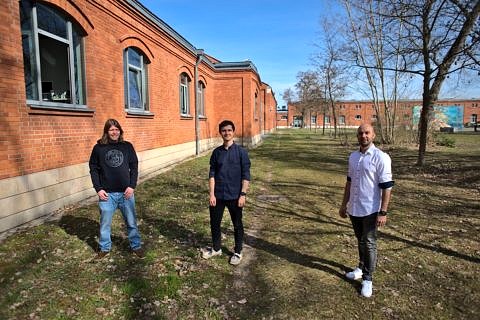
Tubes instead of traces
A start-up trio at FAU has developed a new technology which can produce passive high-frequency components directly from computer models. They have achieved this by combining 3D printing methods with a special metallisation process. Now the researchers will receive 1.1 million euros in funding from the EXIST programme of the German Federal Ministry for Economic Affairs and Energy (BMWi) to develop the technology into a market-ready product.
Radar systems for autonomous vehicles and flight, IIoT sensors, full-body scanners at airports, remote space exploration, data transfer in telecommunications – all of these applications have grown exponentially in importance during recent years. And they all have one aspect in common – the need to transfer large amounts of data quickly via highfrequency electromagnetic waves. Generally, high-frequency modules consist of passive components, mainly sending and broadcasting antennae and traces on planar printed circuit boards, and active components such as integrated circuits that process antenna signals.
These components can be mass produced in standard designs today, however this is a limiting factor in designing new products: ‘Developers design a new module using computers and simulate and optimise different aspects of their design in 3D, for example the radar waves used in a driver assistance system,’ explains Dr. Gerald Gold, mechatronics engineer at the Chair of High Frequency Engineering, FAU. ‘Then they look through racks to find suitable components and may have to adapt their design to the available 2D production technology, which is clearly far from ideal.’
Antennae straight from the printer
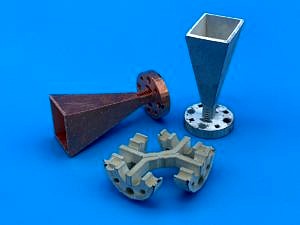
Gold has been working with industrial engineer Mark Sippel and IT communications engineer Konstantin Lomakin at LHFT since 2016 to find an alternative to printed circuit boards by printing components for high-frequency systems directly from the simulation program.
In their method, the components are printed by a 3D printer which uses UV radiation to harden liquid resin layer by layer, eventually forming a plastic body. Finally, the component body is metallised with silver paste to ensure electrical conductivity. ‘It’s a high-precision process,’ says Konstantin Lomakin. ‘We are working with maximum tolerances of five hundredths of a millimetre.’
The new method allows the researchers to move away from the conventional design of 2D printed circuit boards and flat antennae. The new antennae consist of small tubes, which act like resonance chambers. This allows electrical waves of high frequencies to be guided and radiated in the desired spatial direction. Similar to conventional methods, these signals are also processed by a single chip.
‘Our method allows passive components to be produced in almost any form and also sets new standards in terms of frequencies’, explains Mark Sippel. ‘At the moment we are working with 170 Ghz’. As a rule, the higher the frequencies used, the higher the spatial resolution will be – this comes into play in driver assistance applications, for example: ‘If you want to detect a car driving ahead with distance radar, you need a comparatively low resolution,’ says Konstantin Lomakin. “However, parking assistance systems need a much higher resolution in order to detect the height of the curb automatically when parking.’
1.1 million euros from the EXIST research transfer programme.
With their expertise, the three researchers are planning their own start-up for supporting small and medium sized enterprises by simplifying the process of designing high-frequency systems and decreasing time to mass production.
In late 2020, the researchers applied to the BMWi EXIST research transfer programme which supports outstanding start-up initiatives that require costly and high-risk developmental research. Their application was successful and the team received 1.1 million euros in funding on 1 April 2021 to fund four positions and new equipment for a two-year period.
If the initial phase receives a positive evaluation, the start-up team hope to receive additional funding in 2023 to finance and set up a company.
Further information:
Dr. Gerald Gold
Chair of High Frequency Engineering (LHFT)